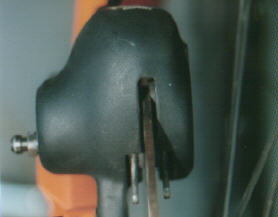
To inspect the rotor, sight straight along the pads of the disk brake mechanism. Slowly spin the wheel while you watch the rotor.Sighting along the rotor while turning the wheel.
The right way to true a rotor is with special tools. If you're an upper-level rider who demands precise performance from your bike, you can buy a truing gauge and drumstix. This set is from MTP (Morningstar Tooling Products).
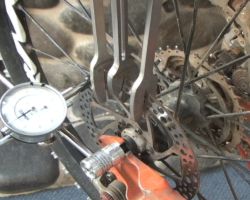
Identify the warped area. Find the spot where the rotor most closely approaches one pad and mark it.
Clamp the disc in an adjustable open-end wrench. Tweak gently away from the direction of the warp, then rotate the wheel and watch for wobble. Continue gentle bending until the warp is minimized.
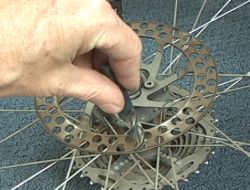
If you're getting a loud "honk" tone sometimes as you apply the brakes lightly, some mechanics recommend that you smooth the edges of the holes on your rotor. (This also keeps the sharp edges from "cheese-grating" your brake pads, so the pads last longer.) Beveling the rotor-hole edges reduces vibration of the rotor, preventing the ugly musical tone that can occur when you apply the brakes lightly.
You can use a rose-head countersink bit with a drill. But I think a nice sharp 1/2" drill bit does the job nicely by hand. A couple of twists for each hole and the edges are smooth, without the risk that you'll drill right through the rotor.
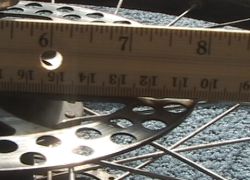
Check the rotor for concavity. This means that the gripping surface of the rotor has been eroded a significant amount away from the former surface. A concave rotor loses braking power, and becomes hard to get out of (and back into) the calipers when you're removing the wheel.
To remove a damaged rotor, remove the wheel from the bike. Using a hex-wrench, remove the retaining bolts from the rotor.
Ideally, you should replace the rotor with a new one. Note the direction of the support struts on the rotor -- they point INTO the brake mechanism in the direction the wheel will rotate. Be sure you put the rotor back correctly, and use a thread-locking compound ("Loctite") on the bolts.